英飞凌
前言
在半导体封装过程中,产品未完全充填是常见的失效模式之一 ,也是影响成品率的最主要的原因之一,造成产品出现未完全充填的原因有很多,如,模具(板)温度,充填树脂的流动性,注塑速度等等。
在塑封设备上,产品在封装过程中,通常是先预热料饼(手动模),目前大多使用自动模,使用的料饼比较小,一般不再需要人工预热。把产品置入模具或是模板,放置模中,再合模,锁模(高压 40~60Mpa)。再把料饼投入注料桶(POT-BUSH),注塑杆以一定的工艺参数下压(或是上压)完成产品的包封。在此部位,即注塑杆与注料桶的设计上有用TEFLON RING,VSPEL RING来作为配合密封,这样就减少了注塑杆与注料桶之间的磨损(其材料一般用ASP-XX,CARBIDE)。目前,封装设备根据产能的需求设计为了有单个注塑杆及多个注塑杆不同的型号
问题介绍
我工厂生产模式是RtR(Reel to Reel),即料盘到料盘,框架为带状,与其他公司使用的为片状形有所不同。 封装设备是多个注塑杆。
首先,要说明的是我工厂设备使用的注塑杆不带有其它密封环,注塑杆与料桶直接配合,它们都使用硬质合金(钨钢)制作,通过精加工使其的配合尺寸公差在0.003~0.007mm之间,其配合的行程较长。
由于配合行程长,及高要求的公差,在使用中出现了问题,即注塑杆在注料桶中卡住,使注塑杆的行程达不到要求位置,树脂没有完全挤压到封装型腔里,出现产品没有被完全包封, 造成未完全充填失效品的产生, 严重时曾发生过注塑杆断在注料桶。
正是由于这样的情况存在,在我厂生产中经常发现产品未完全包封/充填,其封装成品率一直在99.7%以下,其未完全充填失效率达到0.24%
付失效品图.
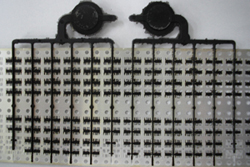
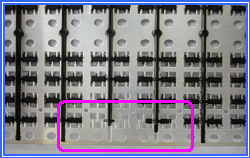
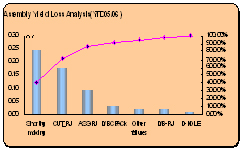
实验(解决方案,新设计)
针对发现的问题对原始设计尺寸进行了研究,同时也与供应商进行联系,共同进行讨论对注塑杆及注料桶改进的问题。经多次讨论后决定只对注塑杆进行改进。
原理分析,外形设计
一般的注塑杆与注料桶用第三材料作密封圈来弥补其配合公差,由间隙配合成为部分过渡配合。
我厂塑封设备的早期注塑杆与注料桶是直接配合(间隙要求为0.003~0.007,如此高要求有另外一个原因是,注塑杆要作活塞作用,利用注塑桶中的空气顶出CULL, 剩余料饼)),配合长度为56mm. (图1))
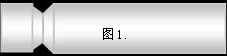
负面问题:
1)在高温下,材料膨胀可能出现由间
隙配合转变为过渡配合,造成注塑杆
卡在注料桶中。
2)一旦有溢料渗入,无法有效排出(即
便有吸尘真空也没有用),容易发生堵塞。
通过以下方法改进注塑杆.
杆身到尾部(头端不改)加入凹槽,减少配合接面.
方案一:.直条槽(图2)
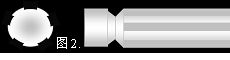
负面问题:
1) 配合,磨损接触面不均匀.
2) 使用中可能会出现侧偏
3) 可能存在温度不均匀.
4) 密封性可能降低.
方案二:螺旋槽(图3)
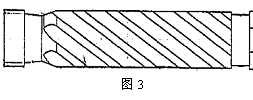
负面问题:
1) 加工难度大
2) 去处面积计算复杂.
3) 加工成本可能较高
优点:
1) 配合,磨损接触面均匀
2) 注塑桶内壁不易堆积污垢, 可以起到刮料作用.
3) 密封性较好
4) 去除面积合理的话,对预热温度的影响较小
从以上分析,最好的解决方案就是螺旋槽的注塑杆。以下的实验是针对螺旋形外形注塑杆的不同螺纹角度进行试验。
试验
通过计算开槽的角度来计算去除面积(但实际是需要配合接触面).其要求为:
1)确保注塑杆在工艺规定的时间内达到指
定的温度,需求最佳的接触面.
2)有效防止由于材料膨胀出现的配合问题
3)密封性不能降低
试验过程:
1. 计算出基本的螺旋角度.
图4. 螺纹角度为X 度
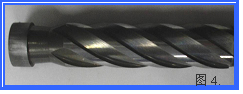
再此基础上进行试验及改进.
图5. 螺纹角度减小 3 度
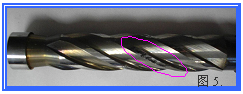
以上修改没有解决问题,仍然发生产品未完全充填,及注塑杆卡的问题. 见图5中的杆上还粘着黑色的树脂.(椭圆圈标出)
图6. 螺纹角度减小 8 度
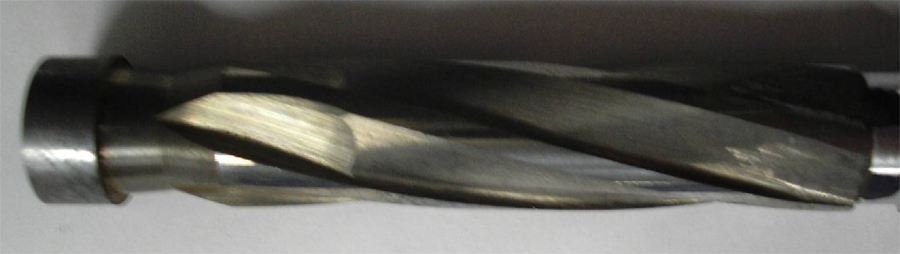
第二次修改后,在试用中倒是没有再发现产品未完全充填,及注塑杆卡的问题, 但在测量注塑杆预热温度时发现比以前低了2~4度. 原因是与料桶的接触面减少了,温度传送面也同样减少了,其影响是在规定的时间内预热温度达不到工艺要求.
同时,也知道了修改的上限角度.
多次使用不同的角度评估其效果.
图7. 螺纹角度减小 5 度
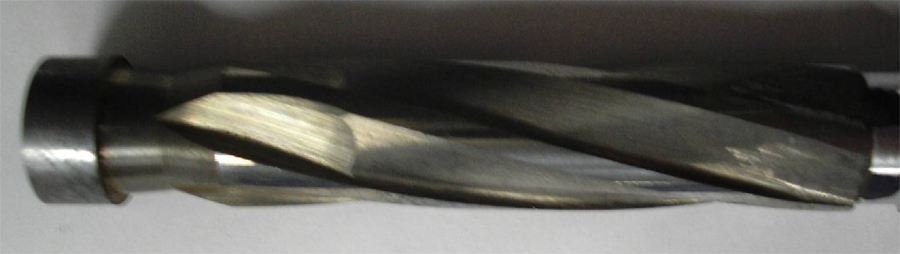
通过反复的试验及尺寸计算,基本确定合理的螺旋角度。在第一次计算出的角度上,把角度减小5 度.
在试验过程中,又发现了更好的改进方案,其尺寸得到进一步优化:
在确定了螺旋角度的同时,对配合的长度也作了相应的优化。不再是原设计时的全尺寸及同公差,而是寻找最恰当的,最优化的配合.如附图8. 确定有效的配合尺寸.
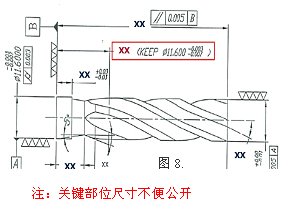
在试验中,通过全程监控, 及时评估,确认达到以下要求:
1) 预热温度达到工艺要求
2) 没有出现注塑杆卡住,及渗漏树
脂.
3) 密封性没有较低,剩余料饼被有效
推出注塑桶.
4) 注塑杆与注塑桶磨损均匀, 同时
确定其使用寿命比较理想,较以往
有所提高.
最重要的是,没有再发现有未完全充填的产品出现,失效率降低.
结果(前后比较)
未充填失效比率图:
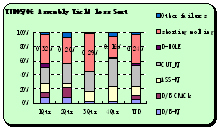
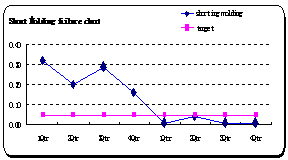
封装成品率趋势图:
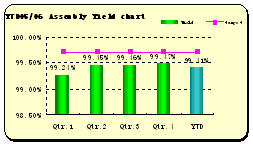
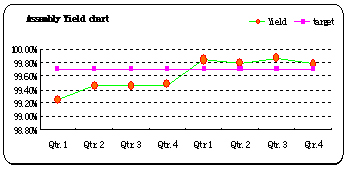
结论
从使用改进的注塑杆后,可以看到图标数据显示未完全充填的失效率已极大的得到减低,成品率达到了目标线上。
就此可以证明: 对注塑杆的改进,尤其是对螺旋角度的确定,及配合尺寸的优化已经达到最优状态.
经过长时间的使用,现在已经确定改进是成功的,同时效果也是显著的, 达到预期目标.同时也得到意外收获,即注塑杆的使用寿命提高30%.
感谢
在此感谢,Mr. Monteiro Rony(ME), Mr. Xi YongJie(PE),以及供应商Mr. Yeo KL, 对在注塑杆改进过程的大力支持。
感谢,Mr. Soh YuenChun, Mr. Lim tian Hing 对我写此文章的指导,以及帮助完成发表。
徐军,半导体封装设备工程师
地址:江苏无锡市-新加坡工业园行创三路8号214028
电话:0510-6610 8721 电子邮件:junn.xu@infineon.com
更多回帖